Noticias
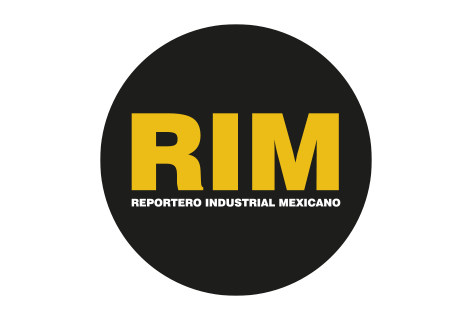
Los robots colaborativos se han inmiscuido en tareas de apoyo para los operadores. Ya no solo basta con pensar en aquellas actividades de alto riesgo o de precisión milimétrica a altas velocidades, sino que ahora el enfoque está en aquellas que representan un bajo valor, tanto en términos económicos como de destreza o toma de decisiones
En la industria automotriz los robots ya tienen más de 50 años realizando tareas catalogadas como súper humanas, relacionadas por lo regular con funciones como cargas pesadas, alta velocidad, precisión milimétrica, mayor repetitividad y con actividades peligrosas o de alto riesgo.
El esfuerzo por liberar a las personas de tareas poco ergonómicas ha abierto el campo de trabajo a los robots. David Ortega, investigador especialista en temas de Robótica Industrial en el Centro en Investigación en Ingeniería y Desarrollo Industrial (CIDESI), asegura que el crecimiento de la robótica en los últimos años es evidente en México y que poco a poco se irán desvelando los casos concretos de inversiones recientes en robótica colaborativa que hoy todavía no se han podido dar a conocer por los propios proveedores de estas tecnologías debido a sus acuerdos de confidencialidad. “Hemos visto, de hecho, un interés creciente en los últimos años por proyectos relacionados con este modelo de automatización”.
Según reportes públicos de la firma ABI Research, en el mercado global de cobots se prevé un crecimiento sustancial en los próximos años.
Aún con el incipiente desarrollo de la economía, se considera que en 2021 se superarán los 600 mdd en ventas, alcanzando 8 mmd para 2030, es decir, un crecimiento anual compuesto de 32.5%.
Comparado con los robots convencionales, los colaborativos están pensados para brindar asistencia a las personas, no para trabajar de manera aislada. De ahí su actual tamaño. Debido a sus características inherentes, las cargas para las cuales están diseñados oscilan entre los 3 y 20 kilogramos, según la marca y el modelo. Abraham Sosa, key account sales manager para América Latina de la firma Universal Robots, explica que el tema de la carga está relacionado con elementos de ergonomía, pero también de seguridad, aspecto fundamental en los robots colaborativos. Los equipos más recientes de este fabricante danés consideran 27 puntos embebidos de seguridad, mismos que incluso están siendo ya normados por la industria robótica.
Por su parte, Salvador Santana, ingeniero de ventas de Robótica de la división de Automatización Industrial en Mitsubishi Electric, explica que, junto con la seguridad implícita en el diseño de los robots colaborativos, se obtienen otros beneficios como el del ahorro en espacio en planta. “El hecho de no tener vallas protectoras nos permite ganar mucha área de piso. Cada cm2 ganado es vital en la manufactura actual, que además se suma a los indicadores de productividad, cuya ecuación considera tiempo y espacio”.
David Ortega, de CIDESI, señala que el desarrollo basado en sistemas abiertos (open source) ofrece un gran potencial para la creación de aplicaciones diversas, agregando mayor facilidad. “Esto permite una suerte de democratización a la hora de desarrollar aplicaciones específicas a partir de los plugins, mismos que las empresas proveedoras utilizan para el desarrollo de programación”.
Ortega hace referencia a la Arquitectura Unificada de Comunicaciones de Plataforma Abierta (OPC UA), que facilita el desarrollo de esquemas de comunicación entre máquinas.
El desarrollo de una arquitectura de programación abierta podría acelerar el despliegue de robots en las plantas de manufactura y esta es una tendencia real. Con la presentación del sistema operativo ForgeOS, de la firma Ready Robotics, se dispondrá de una plataforma de programación para robots con aplicación para diferentes marcas.
Asistencia automotriz
Abraham Sosa trae a la mesa el día que Tesla, debido a algunos ajustes logísticos en la producción del modelo 3, tuvo que traer desde China un lote de cables de un tamaño considerable. Los conectores tenían pequeñas variaciones y los robots resultaron incapaces de manipularlos. Esto causó una reprogramación de los dispositivos y les costó tiempo y dinero que no tenían contemplado. “Se dieron cuenta que estaban sobreautomatizados y que los cambios en lotes de producción podrían tener repercusiones verdaderamente peligrosas”.
Tesla tuvo que patentar un conector para facilitar la automatización en el proceso de ensamble. En el portal de la publicación Electrek se cita este caso con declaraciones del equipo del fabricante de autos eléctricos: “Los cables tradicionales, como los cables de componentes, los cables USB o los cables HDMI, son fáciles de manipular con manos humanas para la conexión con conectores apropiados que están dispuestos en diferentes estructuras o dispositivos. Sin embargo, la instalación de estos cables es difícil de automatizar. Los cables carecen de suficiente integridad estructural y rigidez para ser recogidos, movidos y colocados fácilmente por un brazo robótico. Aunque ciertos cables tradicionales, como los cables USB tipo C, están diseñados para múltiples propósitos (como transmisión de energía, datos y video a través de un solo cable), es posible que las aplicaciones específicas no requieran la transferencia de los tres tipos de información."
El CEO de Tesla, Elon Musk, admitió públicamente que uno de los principales errores cometidos en sus esquemas de manufactura ha sido precisamente querer automatizar tareas en las que el ser humano es mucho más eficiente, como la manipulación de cableado.
Por tal motivo, la robótica colaborativa se presenta en la industria automotriz como un excelente aliado, pues no hace a un lado por completo al operador, pero sí le quita el peso de tareas arduas, monótonas y de alta fatiga.
En 2018, el Foro Económico Mundial advirtió que para 2025 los robots podrían ocupar 52% de las tareas profesionales en el mundo, no obstante, el uso de estas tecnologías podría demandar alrededor de 60 millones de empleos con un nuevo perfil.
Sosa, de Universal Robots, detalla que algunas líneas de ensamble tienen robots colaborativos para tareas de detallado de pintura y pulido. También se les encuentra con más frecuencia en procesos de aplicación de pegamentos, dispensadores de grasa y adhesivos, como aquellos que se aplican a los cristales, que requieren precisión, uniformidad y una alta repetitividad.
Otra de las áreas comunes es la colaboración en metrología e inspección de la calidad, pues pueden detectar variaciones e inconsistencias al incorporar sistemas de visión avanzados. La detección de fugas, identificación de fracturas, detalles de ensamble, como la alineación entre puertas y carrocería, o aspectos de trazabilidad, también son tareas cubiertas por los nuevos colegas cibernéticos. Además de hacerlo con mayor precisión y velocidad, también hacen un registro automático de todos los detalles que van encontrando, lo que facilita análisis posteriores.
Otra de las aplicaciones en ensamble es el atornillado y remachado en zonas de difícil acceso. Durante su recorrido en una línea de ensamble, el automóvil ahora llega a estaciones de trabajo donde, además de personas, se encuentran robots trabajando de manera simultánea, cada uno llevando a cabo las tareas para las que mejor son aptos. En algunos casos, es el robot el que ejecuta mientras el operador solamente realiza acciones de supervisión.
La naturaleza de organismos como CIDESI es trabajar precisamente con empresas para ayudarles a desarrollar soluciones que les permitan mejorar sus esquemas productivos. En el caso de empresas automotrices, David Ortega explica que han desarrollado diversos proyectos y que, en ocasiones, tienen que partir de cero. “Tuvimos un caso en Monterrey que requería de un proceso de inspección que no estaba disponible en México. Revisamos varias tecnologías para generar aplicaciones diversas y terminamos incorporando robots colaborativos con visión artificial y sensores diversos como movimiento y proximidad. Este caso es un buen ejemplo de lo que en general ocurre. En las empresas no se debe pensar en un robot colaborativo como requerimiento, sino en la solución de automatización a partir de la cual estos equipos pueden ser incorporados”.
Promesa de flexibilidad
La manufactura moderna cambia muy rápido y requiere de tecnologías que, de igual manera, puedan ser adecuadas más rápido a cambios de configuración. Los robots colaborativos no solo son más ligeros (alrededor de 40 kg), sino que además se conectan muy fácil (con corrientes de 110/220 v) y pueden configurarse de manera ágil e intuitiva (gracias a programación abierta y de objetos).
“Los cobots son la opción ideal para líneas semiautomáticas y mixtas”, asegura Salvador Santana, de Mitsubishi. “Este puede considerarse como el primer requisito para un robot colaborativo. El segundo es la carga útil, considerar tanto la pieza como el gripper para la aplicación buscada. Esto determina el tipo de robot y sus dimensiones. Finalmente, se tiene que considerar su rango de operación, el alcance máximo y radio de acción. Con esto se determina la capacidad del robot para completar tareas de rutina cada vez que llega a la misma ubicación”.
La precisión de estos equipos alcanza ya los 0.3 milímetros, un rango que le permite cubrir muchas aplicaciones industriales.
David Ortega, de CIDESI, considera que México se encuentra todavía en pañales en temas de robótica y de infraestructura de Industria 4.0, por lo que el potencial es muy alto, pero aún queda mucho qué hacer en materia de educación para, por un lado, discernir entre la inversión y el retorno de esta, así como para formar la “mente” de obra calificada necesaria para operar y supervisar líneas de producción altamente automatizadas o semiautomatizadas.
“Los nativos digitales se adaptarán más rápido a estas nuevas tecnologías, pero el proceso o salto de generación a nivel piso será algo que los directores de manufactura tendrán que enfrentar con responsabilidad”, sentencia Ortega. “Me ha tocado impartir algunas pláticas en clústeres y en Universidades, lo que me ha permitido observar que existe una gran brecha aún entre empresas grandes y empresas medianas y pequeñas de nivel Tier 1 y 2”.
Sin embargo, es cuestión de tiempo para que los brazos artificiales llenen los espacios de la cotidianidad fabril a lo largo de la cadena de valor automotriz.
Otros artículos de interés
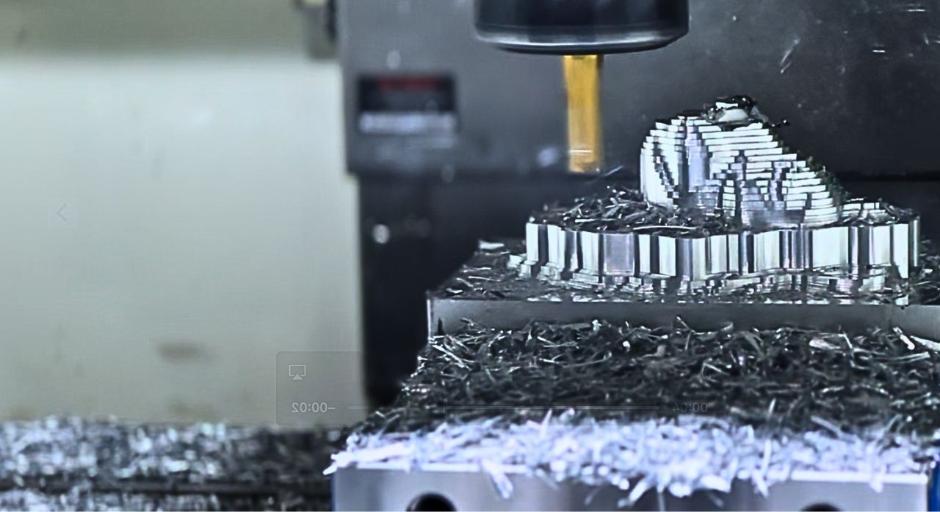
Herramientas de corte: Mayor valor para el maquinado aeroespacial
La industria del maquinado para componentes aeroespaciales en México continúa desarrollándose y

Lubricación: generador de eficiencia en planta
La lubricación influye directamente en la vida útil de maquinaria y en
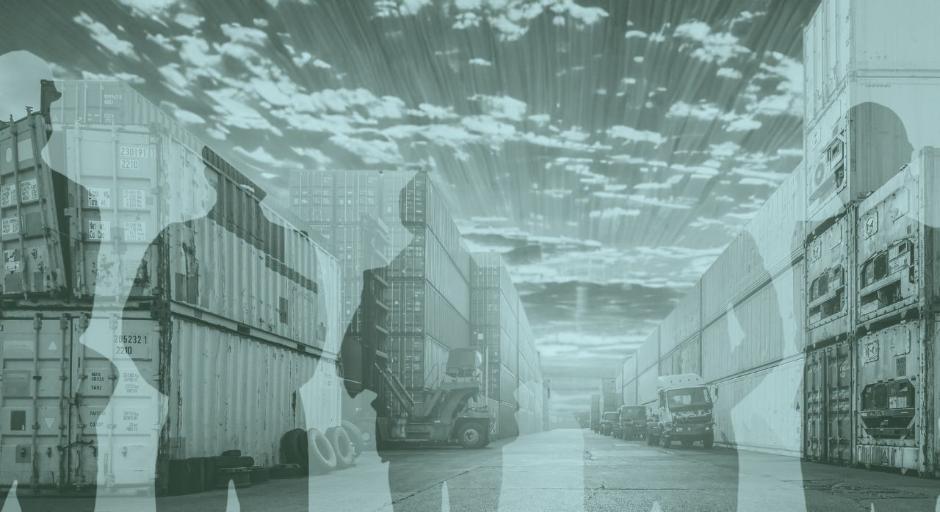
Ante aranceles, ¿qué papel juegan los organismos bilaterales?
La presión política sobre el comercio internacional ha incrementado de manera notable

La digitalización en mantenimiento reduce fallas en planta
En la industria actual, mantener las máquinas en funcionamiento no basta. La transformación
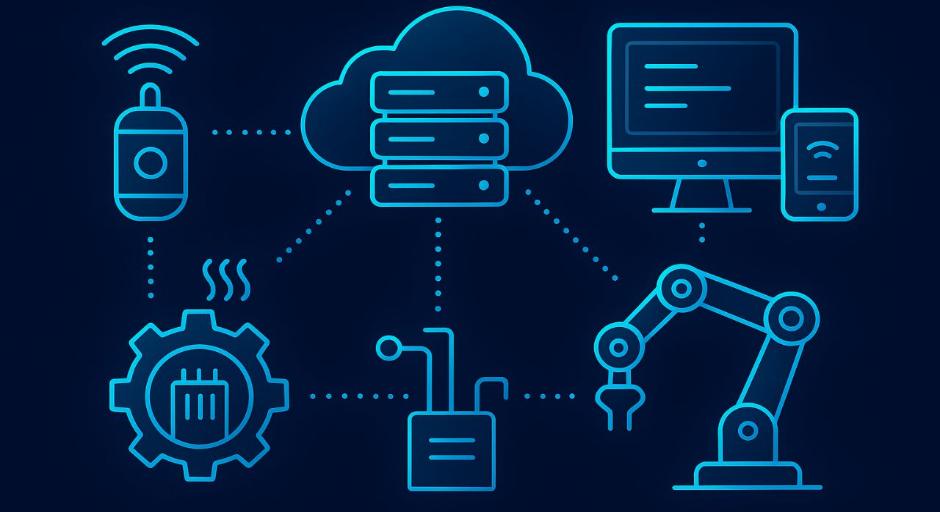
Se transforma la seguridad industrial con tecnología inteligente
La seguridad en las plantas industriales mexicanas ha vivido una transformación impulsada
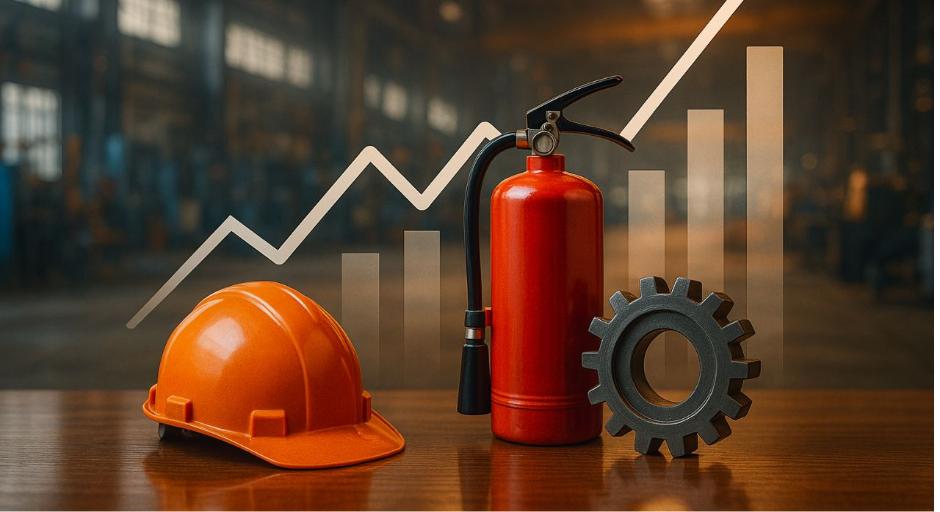
La seguridad industrial tiene un valor estratégico
La seguridad industrial es, y deb ser vista, como un componente estratégico